Top Five Reasons Behind Construction Rework in Nigeria
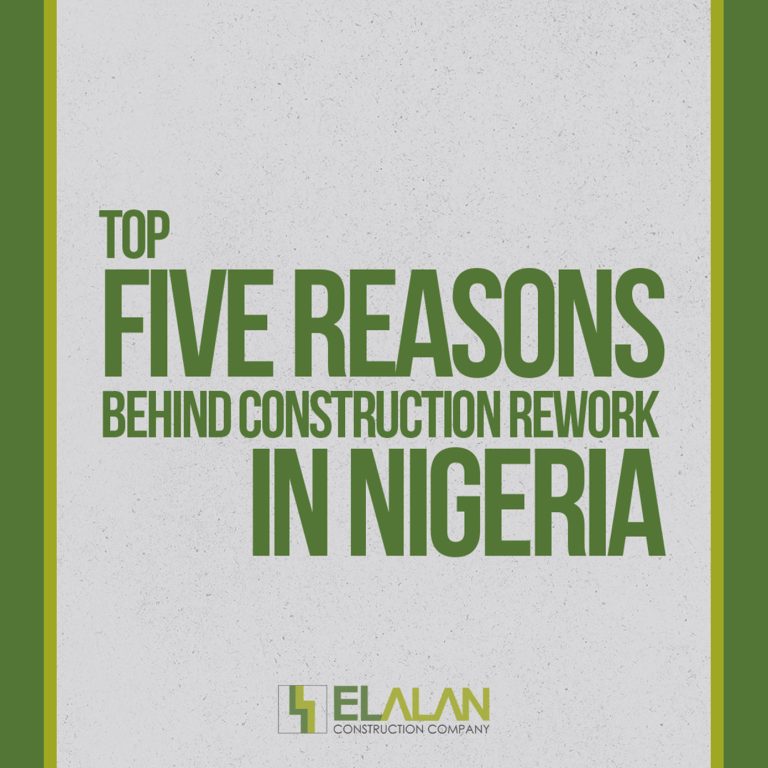
Rework in construction projects can be a significant issue for both contractors and clients. It refers to the need to redo or fix certain portions of the work, leading to added costs and delays. Unfortunately, rework is a common challenge faced by construction firms in Nigeria. Understanding the main causes of rework and how to prevent them can help ensure the successful completion of a project.
Here are the top five reasons behind construction rework in Nigeria, along with solutions to avoid them.
1. Poor Planning and Scheduling
One of the primary causes of rework in construction projects is poor planning and scheduling. When projects fall behind schedule, work is often rushed to catch up, leading to mistakes and quality issues. Approximately 25% of rework is related to scheduling problems. To avoid this, ensure that all tasks are properly planned and that there is adequate time allocated for each phase of the project. Regularly monitor the project’s progress and address any potential delays before they snowball.
2. Design Issues and Errors
Design-related rework often occurs due to omissions, errors in the design plans, or agreed-upon design changes. While design errors are sometimes beyond the control of contractors, contractors in Nigeria can help identify potential issues during the planning, design review, and bidding stages. Ensuring clear communication with designers and architects and conducting thorough reviews of design plans can help prevent costly errors and rework.
3. Construction Errors
Rework is frequently caused by construction errors, which can stem from a variety of issues, such as budget constraints, layout problems, or misinterpretation of plans. The main factors leading to construction-related rework include:
- Misinterpretation of plans and specifications: Ensure all team members fully understand the plans before starting work.
- Inadequate supervision: Having experienced supervisors on-site helps prevent mistakes during construction.
- Inexperience or inadequate training: Provide adequate training for workers to ensure high-quality work.
- Quality management issues: Implement a strict quality control process to minimize errors and prevent rework.
4. Equipment and Material Defects
Sometimes, work is completed according to plan, but the materials or equipment used don’t meet the required specifications, leading to rework. This can include using concrete that doesn’t meet strength requirements or installing windows with the wrong type of glass. To reduce rework caused by material defects, always ensure that all materials meet the project’s specifications before work begins, and choose reliable suppliers with high-quality products.
5. Fabrication Issues
Pre-fabricated components can save time on construction projects, but they may also contribute to rework if they arrive on-site with defects or issues. Fabrication problems, such as improperly made parts, can cause delays and may require rework to meet the project’s standards. To avoid this, carefully inspect pre-fabricated components before they are delivered to the site, and establish quality control measures for the fabrication process.
Conclusion
Rework is a common issue in construction projects, but with proper planning, attention to detail, and effective communication, construction companies in Nigeria can significantly reduce the risk of rework. By addressing common causes like scheduling issues, design errors, construction mistakes, material defects, and fabrication problems, contractors can improve efficiency, reduce costs, and complete projects on time.
Leave a Reply